Back to the fuselage / tail cone attachment process. As you may recall, there was some problem getting things to align at the aft baggage bulkhead when Nick & I clecoed the tail cone to the fuselage. To bring you up to date, here’s my posting to VAF:
Well, it looks like I got things taken care of. I ordered new roll bar bases in anticipation that I would need to remove/replace them to change the angle of the roll bar, but I will be able to return them to Van's. I removed the F-1254 support frames and drilled out the rivets securing the roll bar to the roll bar bases. Viola! The roll bar promptly cooperated with rotating forward and straightening out the F-1207 baggage bulkhead. I could not see any appreciable movement at the roll bar bases and could see daylight when I looked through the sides (left to right of the entire plane, not just each roll bar base.)
I fully clecoed the turtle deck skins to ensure that everything aligned properly. I placed two rivets on each base, and was unable to move the roll bar with some vigorous manipulation. Holes were still well aligned, so everything got riveted back together and I'm back on track.
Conclusion: My error when I situated the roll bar. It was a year ago, but I think I had to use a great deal of verbal lubricant (4 letter words) to get the bar to fully seat. That should have clued me that this was a critical junction and I should have been more careful about finishing the rest of the aft structures to ensure good fit elsewhere. As it was, I didn't notice that the baggage bulkhead was bowed toward the rear when I built that section last year.

new & improved fitting of aft baggage bulkhead and tail cone
Step 1 is deceptively simple. Rivet the shear clips. Well, the shear clips are now inside the back of the plane. This was my first adventure climbing into the “the hole”. While I was there, I routed the pitot tube through the loose tie wraps (2 years ago!) but discovered that the DB9 connector for the data cable won’t fit through the tie wraps. I’ll replace them when I route the rest of the cables to the ADARHS.
Step 3 is also deceptively simple, with only a few words more than “rivet...” It took about 2 hours to remove each cleco, ream, rivet & move on until all were done. Oh, well. Lots of work, lots of smiles.
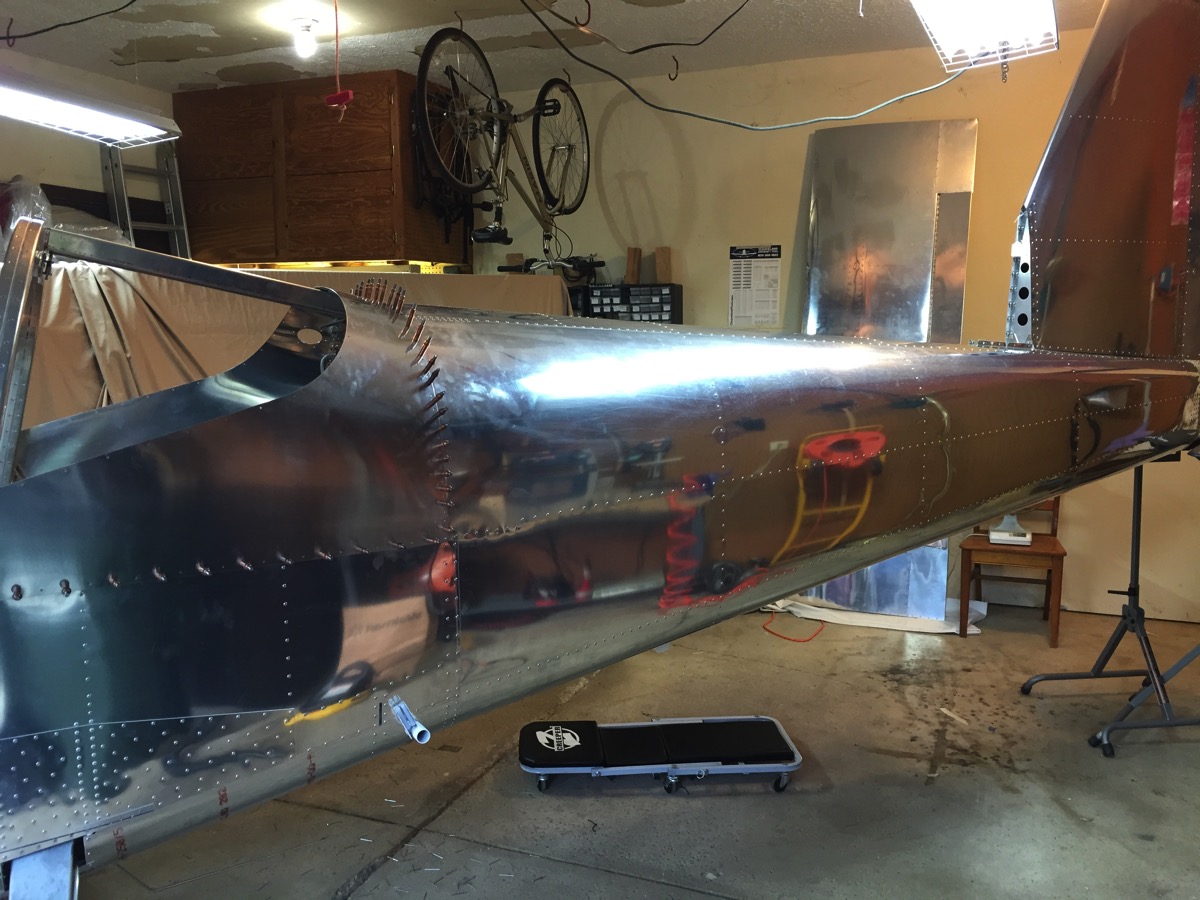
Tail Cone installed on Fuselage